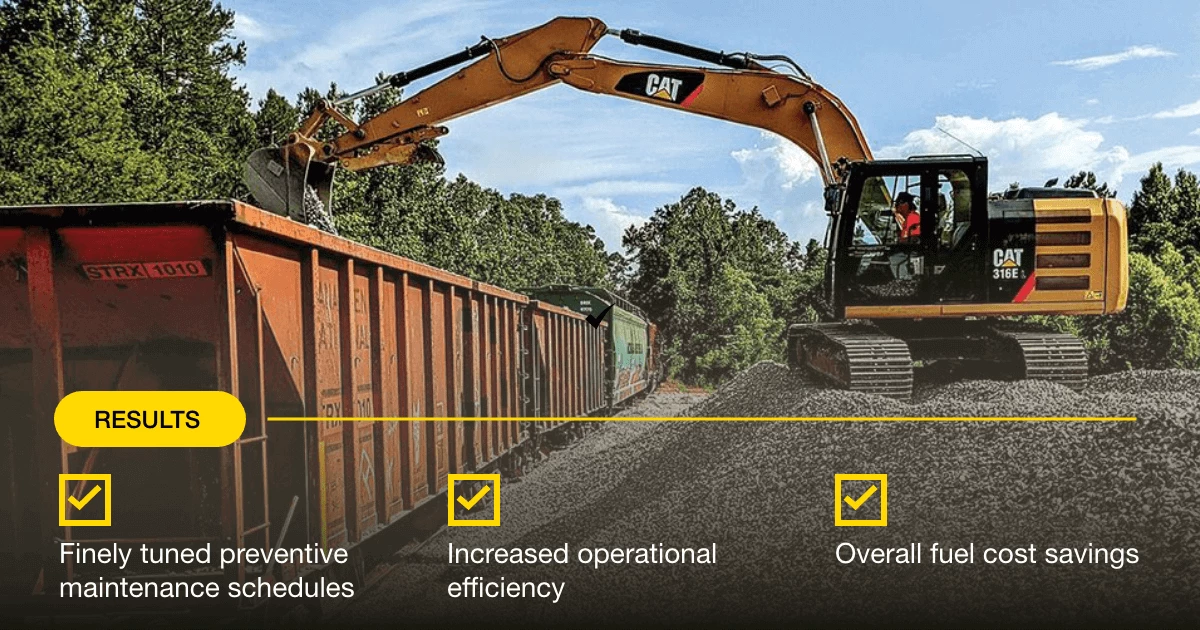
WATCO'S TELEMATICS JOURNEY WITH TN360
Over the last 40 years, Watco has grown from a single switching operation into a logistics powerhouse with locations spanning North America and Australia. Their operations encompass an unmatched network of short line railroads, terminals and ports. However, what truly sets them apart is their commitment to safety, efficiency, and sustainability.
Through their investment in the latest telematics tech, the Watco team have been able to take significant strides forward. This started with their use of video telematics, where they have been able to protect their drivers from false claims, and more recently expanded into their terminal facilities, where they have implemented an asset management platform to help them improve the efficiency of their transloading service.
The terminal facilities are the hub of the logistics process, where materials are received and stored, and then shipped to the different customers they have been sold to. With many of their customers requiring the raw materials to sustain production lines, a disruption to delivery schedules can come at a high cost, and this drove the Watco team to find a solution that ensured their team always had the equipment to get the job done.
INCREASING UPTIME WITH DIGITAL MAINTENANCE
Managing hundreds of assets maintenance schedules is no doubt a daunting task. Watco had found themselves over maintaining some equipment, while also under maintaining others. The game-changer came with the integration of TN360 ACM into their electronic maintenance platform. Shifting from the traditional calendar-driven schedules, Watco moved to a data-driven approach. By automatically pulling engine hours and odometer readings, they could create finely tuned preventive maintenance schedules that cut unnecessary maintenance visits, leading to real world savings and increased equipment availability. The improvement in visibility is one of the biggest impacts that Eli Demmer, Director of Business Solutions, has seen. “We didn’t have good visibility of the current runtime across our equipment, and we were bringing in equipment for maintenance on a more frequent basis than needed. Moving from a periodic maintenance schedule to a data driven schedule has already resulted in significant maintenance cost savings.”
Watco's serious commitment to safety shines through their adoption of digital pre-use inspections. Moving away from the traditional paper-based methods, the team now receive real-time notifications of potential safety concerns, allowing for swift corrective action. This transition from manual to digital was a key step forward in operator safety, that was recognized by Eli. “One of the key reasons for digitizing our maintenance programs was to ensure that we’re doing everything we can to keep our operators safe. The digital inspections ensure that we’re picking up small issues with our equipment and quickly getting them resolved.”
PRECISION IN TURN TIME MANAGEMENT
Turn times, the period from unloading materials off ships to their delivery at customer sites, is a key marker of operational efficiency. With many of Watco’s customers requiring the raw materials being shipped to sustain production lines, any delay in delivery could have a costly impact. With the help of TN360 ACM, Watco now has the visibility into their turn time efficiency, which is helping them to continually improve processes, minimize the risk of preventable delays and protect them from delays that are outside of their control.
In one case the Watco team were able to use the data to showcase that a delay was caused by issues outside of their process and were able to gain significant chargeback recovery.
“With many of our customers requiring raw materials to maintain production, ensuring that we have efficient turn times is crucial,” explains Eli. “The visibility that we now have enables us to accurately track the entire process, helping us to identify areas of inefficacy and when needed, prove service delivery.”
FUELING EFFICIENCY AND SUSTAINABILITY
The integration between TN360 ACM and Gasboy has also provided invaluable insights into fueling practices and consumption patterns. It ensured authorized fuel usage and accurate fuel selection while offering a detailed view of fuel efficiency across their fleet. This comprehensive view of fuel consumption played a pivotal role in cost management. “Fuel is one of our largest costs and we needed to get better visibility of how the fuel was being used. The solution has helped us improve security and we are starting to realize cost savings.” Noted Eli.
The impact of the integration is going beyond cost savings and Watco is using the data to support their sustainability initiatives, utilizing fuel data to populate Electric Vehicle (EV) feasibility studies. “We have been able to use the fuel data to validate cost savings for an EV feasibility study for our yard mules, the data has really helped us make the decision on sourcing more EV’s in the future”
SUMMARY
Watco's journey with telematics, powered by TN360 ACM, has helped fuel their success across their entire business, from driver protection to terminal optimization. The evolution of maintenance practices, inspections, turn time management, and fueling protocols highlights the impact of integrating technology to simplify and streamline processes. As they continue to navigate new horizons, their journey highlights the power of technology for a brighter, safer, and more efficient future.